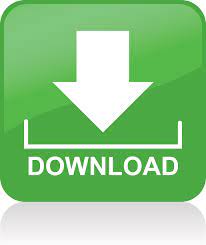


The task group directed the Rhino Team to develop a white paper before the requirements were put into IPC J-STD-001. The task group quickly realized that industry needed a technical explanation of the requirements and guidance to help with implementation. The task group determined that a qualified manufacturing process was required for manufacturers of Class 2 and Class 3 products. Over the course of several years and presentations to the IPC J-STD-001 task group, new cleanliness requirements were beginning to emerge. This team included technical subject matter experts from aerospace, materials, automotive, and commercial companies. From this information, science tells us that the ROSE test is inadequate in these situations.Ī different method or combination of methods for establishing cleanliness of an assembly is needed to provide “objective evidence.” That knowledge and understanding led to a small group of dedicated volunteers who named themselves the “Rhino Team” to look at the requirements of IPC J-STD-001 and make recommendations for change.

The ROSE test is based on spraying/immersing the board into a 75% alcohol/25% deionized water solution. Many datasheets indicate that the new flux chemistries cannot be brought into solution with alcohol or water. With the complexity of assemblies increasing and flux chemistries and cleaning solutions changing, the ROSE test-originally developed in the 1970s as a process control method for rosin-based fluxes-was not an adequate test for acceptable levels of ionic residues on the majority of the new flux chemistries. This was conducted using Resistivity of Solvent Extract (ROSE) testing per IPC-TM-650, method 2.3.25. Leading up to that time, for many years, vast facets of the industry utilized a requirement of 1.56 µg/cm 2 NaCl to determine acceptable cleanliness of printed circuit assemblies. This document, a white paper, was released to help the industry understand new cleanliness requirements in the G revision of IPC J-STD-001 Requirements for Soldered Electrical and Electronic Assemblies. This white paper, prepared by a subtask team of the 5-22A Task Group working on J-STD-001G Am 1, explains the history behind the changes and provides the reader with the context by which the new requirements should be viewed.IPC-WP-019, “An Overview on Global Change in Ionic Cleanliness Requirements,” was initially released in August 2017. Highlights of this amendment include, unless otherwise specified by the User, a requirement for Manufacturers of Class 2 and Class 3 product to quality soldering and/or cleaning processes that result in acceptable levels of flux and other residues where "…the use of the 1.56 μg/NaCl equivalence/cm2 value for ROSE (Resistivity of Solvent Extract), with no other supporting objective evidence, is not considered an acceptable basis for qualifying a manufacturing process…"Īccompanying this product will be a copy of IPC-WP-019A, An Overview on Global Change in Ionic Cleanliness Requirements. IPC J-STD-001D-Am 1 provides the first major revision of the J-STD-001 cleanliness requirements in over 25 years and changes how the industry will address cleaning and residue requirements.
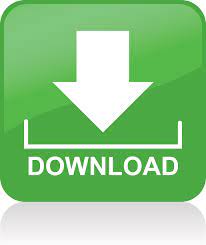